Manganese-rich cathode chemistries: The once and future king?
VW's embrace of manganese-heavy cathodes may be a harbinger of things to come in the battery industry.
During its Power Day event, Volkswagen surprised the battery industry in many ways. But one of the most significant announcements was its intention to incorporate high-manganese cathodes into its future mainstream cathode chemistry. This contrasted with Tesla’s recently-announced plans to push for high-nickel cathodes. In fact, no major automaker had previously announced such a large-scale commitment to manganese-based cathode chemistries.
James Frith from BloombergNEF has even speculated that "the 2030s could be the decade of manganese", a prediction which reflected the belief that manganese chemistries still faced major barriers to commercialization. But VW’s announcement suggests those barriers may be falling sooner than expected. So what are these challenges, how has VW addressed them, and what role will high-manganese content cathodes play in the market as a whole?
The underlying reason for manganese
As can be seen from the chart above, global manganese availability is at least 10x -100x greater than nickel and cobalt. Add to that the density of the ores and the ease of the extraction process, and manganese is in itself a much easier metal to extract as compared to nickel or cobalt.
We’ve all heard the stories of how cobalt extraction paints picture of a medieval as well as dystopian future, so much so that batteries made from this metal should be termed as Blood Batteries. In addition, 80% of the world’s reserves are concentrated in the Democratic Republic of Congo and that China utilizes almost 90% of all that cobalt; this reveals how constrained the supply chain really is (or how favorable it is to China).
Enter manganese, the savior. Manganese is the free market specialist of all battery metals. Readily available, easily extractable and widely distributed. Can there be a more democratic metal in the battery space?
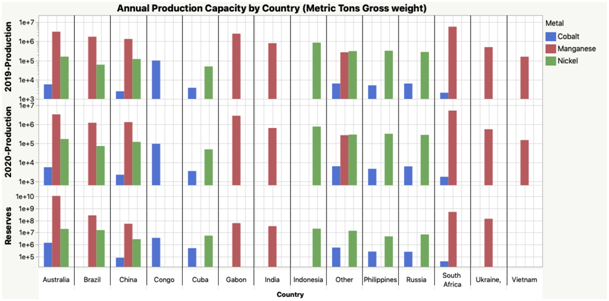
From an annual production capacity as well as the reserves of manganese present, one can clearly see how evenly it is distributed across some of the largest holding countries. Manganese is heavily used in the iron and steel industry; hence, the supply chains are waiting to be tapped into.
Manganese-rich cathode classes
The majority of cathode active materials that have been commercialized in Li-ion rechargeable batteries can be split into three classes based on their crystal structure: that is, the chemical arrangement of the atoms in the material. Remarkably, the discovery of the three classes can be traced back to the labs of Prof. Goodenough, which earned him the Nobel Prize in Chemistry in 2019. These categories also apply to the different Mn-rich cathodes that have been attracting the attention of researchers and industry. Each class has its perks but also comes with different issues that scientist and engineers need to solve before we see a VW ID.3 running on Mn-rich cathodes.
Mn-rich layered cathodes: replacing the expensive cobalt and nickel
Layered structures have dominated the market ever since Sony first introduced the Li-ion battery in their video cameras. The most basic layered cathode is the cobalt oxide LiCoO₂ (LCO) but the supply chain issues with cobalt have steered the industry towards compounds that replace part (or even the totality) of cobalt with more abundant nickel, manganese, and aluminum. Replacing cobalt with these lighter elements also comes with an increase in capacities and cathode voltages, although at the expense of stability. Nowadays the standard in the EV industry is nickel rich compounds like NCM (lithium nickel cobalt manganese oxide) and NCA (lithium nickel cobalt aluminum oxide). Although more abundant and cheaper to mine, nickel could suffer at some point from supply constraints given the exponential raise in demand.
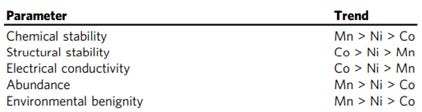
What happens if all the cobalt and nickel are replaced by manganese? Although scientists have tried to synthesize layered lithium manganese oxide (LiMnO₂), the lower bonding forces of the Mn atoms prevent it from crystallizing in the layered structure. Producing a stable Mn-rich layered cathode therefore requires the inclusion of another transition metal that stabilizes the structure. Scientists have successfully demonstrated layered cathode materials with mixtures of Mn and Ni in ratios up to 7:3. This type of Mn-rich layered cathode is commonly associated with an excess of lithium in the material (of about 20%), which allows a further increase the capacity. These materials show energy densities comparable or better than standard NCMs at a considerably lower price. They are also much safer due to the lower chemical reactivity of manganese.
The main factors holding back wider adoption of manganese-rich cathodes have been that they suffer from poor cycle life and thermal stability. This is due to the relatively weak Mn bonding. As a result, manganese tends to leach out of the cathode and poison the anode, degrading the battery performance.
However, great progress has apparently been made in mitigating this problem. For example, the chemical company BASF has been working hard on this type of materials, developing additives and coatings that improve the cycle life, energy density and thermal stability of Mn/Li-rich cathodes. They recently showed an NCM-307 (30% Ni, 0% Co, 70% Mn) chemistry with cycle stabilities above 1000 cycles at room temperature and an energy density at the same level as the popular NCM-622.
Mn-rich spinel cathodes: powering the first-gen Nissan Leaf and the future superbatteries
In contrast to the layered oxide family, the class of spinel cathodes has as its poster child the Mn-rich LiMn₂O₄ (typically abbreviated as LMO). The three-dimensional spinel structure allows faster movement of the lithium ions – faster charge/discharge – and offers higher operational voltages, above 4 V, with fewer safety concerns. And of course, the all-Mn composition has a significantly lower raw material cost. However, the 1 to 2 ratio of Li and Mn has a detrimental effect on the capacity in comparison to layered oxides (33% less) and the cycle life is severely compromised by structural transformations and dissolution of Mn in the electrolyte.
LMO went through its golden age together with the first wave of modern EVs. The first-generation Nissan Leaf used a 24kWh LMO-based battery, but the company switched to a NCM-based chemistry in its second generation due to the decrease in price and performance improvements in the NCM cathode class. Nowadays LMO finds its major use in power tools that require high power. For automotive applications some manufacturers still use LMO as part of a blend with other chemistries like NCM in order to increase the cathode voltage and its power rate.
The rising star of the spinel cathode class is the high-voltage LiNi₀.₅Mn₁.₅O₄ (LNMO) cathode, with 75% Mn and 25% Ni. The substitution of 25% of the Mn for Ni allows increasing the operational voltage to 4.7 V (0.8 V above that of LCO), and therefore increasing the energy density, while retaining the high power capabilities of the spinel class. However, like LMO, the main challenge of the LNMO chemistry is the cycle instability associated with the high manganese content. Moreover, the higher operational voltage, although beneficial for the energy density, is a major problem with conventional liquid electrolytes, which decompose at those high voltages and affects the cathode/electrolyte interface. Interface engineering and new electrolyte formulations are necessary for practical application of this family of cathodes.
Aside from all the work done on LNMO by researchers, several companies have turned the spotlight onto this material as well. One of these companies is Haldor Topsoe, a Denmark-based company that has developed a proprietary coating for LNMO as well as new electrolyte formulation that allows enhanced cycling life. The company has shown practical capacities of about 110 mAh/g with a cycle life of 500 cycles. Haldor Topsoe argues that they can cut down the cost of the cathode material to half the price of a standard NCM. They also claim that their LNMO material is processable in water solutions, avoiding the use of expensive and toxic solvents like NMP.
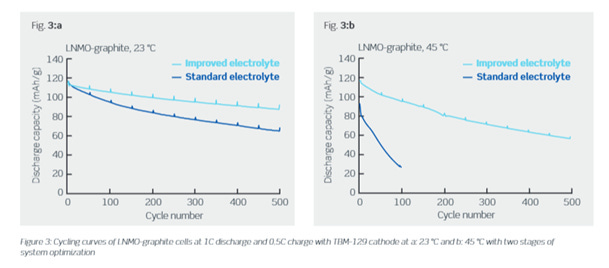
The Canadian company Nano One is also actively working on the development of stable LNMO with their proprietary production processes. The company has also patented a surface treatment for LNMO that mitigates instabilities. They have shown LNMO batteries with a cycle life of about 800 cycles with a solid electrolyte. In fact, Nano One has been partnering with VW since 2019 for the development of this class of materials. Besides the partnership with Nano One, VW and its subsidiary Scania have a close research collaboration with Uppsala University in this direction. In fact, several research papers have been published with shared co-authors from Uppsala University, VW and Scania. All in all, there seem to be strong hints that LNMO is the material that VW is eyeing for their next-generation of batteries.
The incompatibility of high-voltage cathodes with liquid electrolytes could become a problem of the past with the advent of solid-state batteries, which VW considers the endgame of their battery development strategy. Solid electrolytes in general have a wider voltage stability window, allowing operation of high-voltage cathodes without interface degradation. Researchers at Oak Ridge National Labs have demonstrated that a solid-state microbattery with LNMO can be cycled for over 10,000 cycles with over 90% capacity retention. And as the Jagdeep Singh (CEO of VW’s solid-state technology partner QuantumScape) has pointed out, their solid state electrolyte electrically isolates the cathode from the anode, enabling the use of a range of high-voltage cathodes that would have previously been impractical.
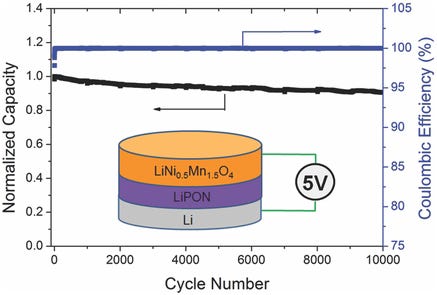
Mn-rich olivine cathodes: a better alternative to LFP?
Polyanion compounds (with more than one negatively charged element, for example oxygen and phosphorus) with an olivine structure have also claimed part of the Li-ion cathode market. Lithium iron phosphate LiFePO₄ (LFP) is the main contender of this class of cathodes. LFP is popular for its low material cost (iron is orders of magnitude cheaper than cobalt), easy processability and long cycle life, although at the expense of a low operational voltage (3.4 V) and low energy density. Despite these drawbacks, it has seen wide adoption in grid storage solutions and low-end EVs, such as the China-made Tesla Model 3 and other affordable Chinese EVs. Volkswagen has also indicated that they will begin using LFP cathodes in their low-cost EV segments.
Scientists have shown that LFP can be improved by partially substituting iron for manganese. On the lab bench, lithium iron manganese phosphate (LFMP) has shown operating voltages of 4.1V, which increases the energy density by up to 20% with respect to standard LFP. However, this compound suffers from poor charge transport, limiting the charge/discharge rate capabilities.
Dow Energy Materials patented in 2012 a functional LFMP cathode material but didn't succeed in bringing this material to market. According to Roskill Research, other companies working currently on the development and commercialization of LMFP are the Japanese Sumitomo Osaka Cement, the Taiwanese HCM, and the British Johnson Matthey. Customcells offers LFMP as an option for their customized batteries.

The bottom line
The recent developments and refinements to manganese-heavy cathode chemistries are apparently accelerating the timeline for widespread industry adoption. A gigantic, established automaker like Volkswagen is fundamentally a conservative organization; their bold push into manganese cathodes would not have been made if they didn’t have full confidence that the major technical challenges had been sufficiently addressed. Their planned rollout for their unified cell architecture and chemistry is slated for 2023, the blink of an eye in mass manufacturing terms.
Given that, we may see the rest of the industry begin to shift quickly towards cobalt-free, high-manganese chemistries as well. The economic advantages of cutting out cobalt and reducing nickel content are too persuasive. These substitution effects may significantly transform the trajectory of the underlying commodities markets, relative to expectations of even a few years ago.